Speedboost
Exergen IRt/c™ non-contact temperature sensors can push production line performance to record highs and give an instant boost in start-up speed. Dr. Pompei has derived a mathematical model to describe the thermal processes that allows you to maximize the speeds of these processes.
Infrared temperature measurement methods of production processes are limited to material surfaces, and thus have a serious limitation in thermal process monitoring, particularly when considering speed increases. To overcome this limitation, a heat balance equation is derived in which the material surface temperature data is combined with other non-contact temperature data to calculate the internal temperature of the product, which in turn is used to optimize control to increase speeds.
The model results are in agreement with experimental data in several industries, where hundreds of actual installations of such non-contact systems are successfully increasing production speeds. The method can be extended to any thermal process and examples for food processing, printing, and laminating are given.
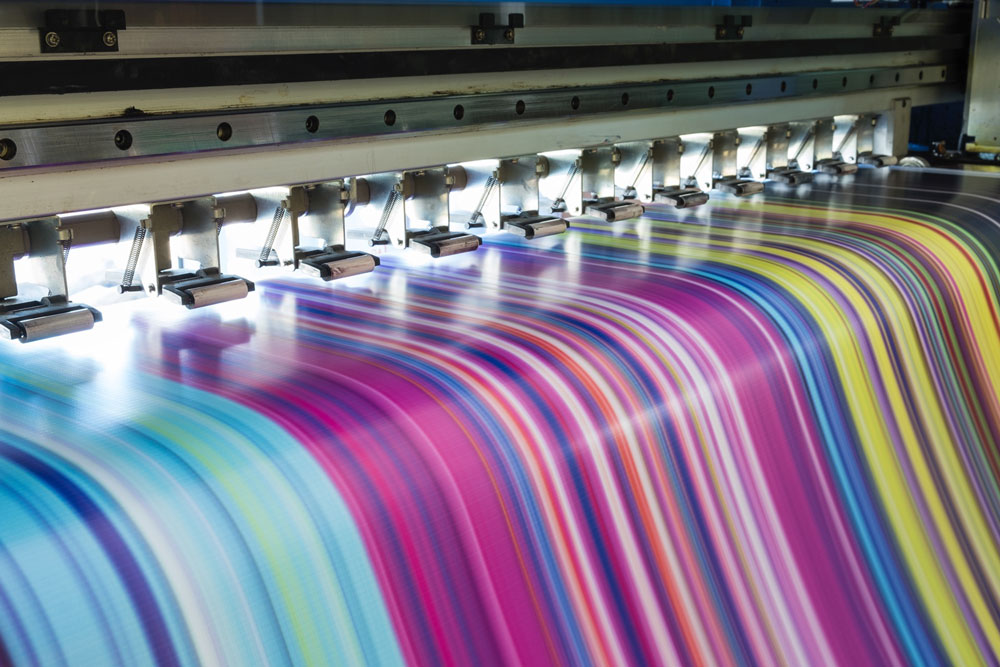
Presentation on Speedboost
Download our presentation on the Speedboost. In this presentation, we give different kind of examples on how to use the speedboost in laminating, drying and heat sealing.
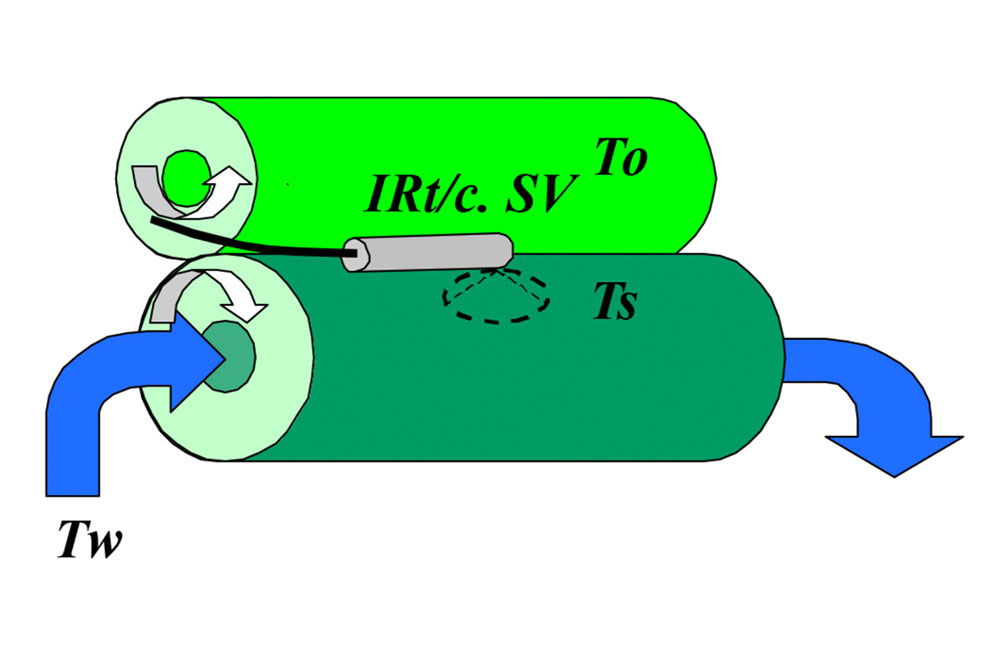
Tech Note #100
By Francesco Pompei, Exergen Corporation
At the heart of waterless printing is the requirement for accurate temperature control of the ink roller system due to the importance of maintaining proper viscosity. A significant barrier to improvement in the quality of ink temperature control for waterless printing systems is the delay caused by the mass of the roller, especially when increasing speeds.
Water-cooled systems are particularly subject to this delay since the roll is cooled from the inside, and the entire mass of the roll must change temperature in order to control the surface, where the ink properties are, of course, determined. Air-cooled systems are less influenced by the delay, but still require an optimal control strategy to maximize speed.
At the heart of the temperature control are non-contact infrared sensors that are designed specifically for the waterless printing application. One such model is the IRt/c-WP series from Exergen, which is the most accurate available. The discussions below use these sensors.
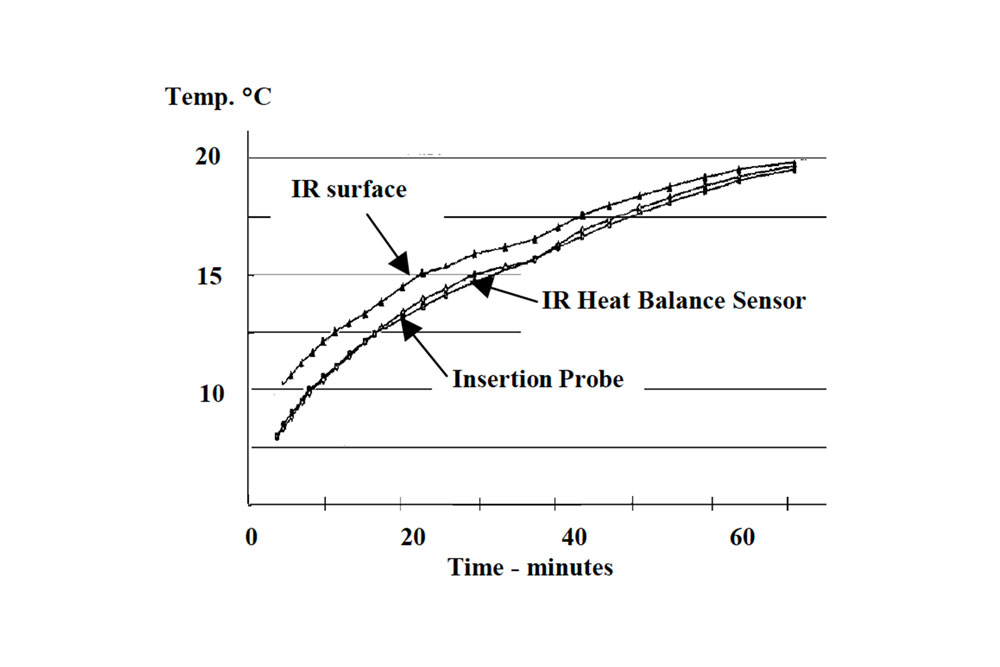