Value of testing PCB
The value of testing printed circuit boards using test fixtures and infrared sensors
PCB Market
The printed circuit board (PCB) Market size is large, it surpassed USD 75 billion in 2021 and is expected to exhibit a CAGR of over 5% between this year (2022) and 2030. While often obscured from sight, PCBs play an essential role in our everyday live, constituting the electronic back bone of many appliances we daily depend on.
Communications (business/retail/computers/telecom) together account for around 60% of the global PCB market and are expected to retain the dominance. PCB’s application in the automotive industry is expected to be the fastest-growing segment in the years to come due to the growing integrated and sophisticated features required in modern vehicles. GPS navigation system, anti-lock brake system (ABS), ECU systems that control engines, and many safety and security features all require PCBs.
Challenge of reducing costs while increasing quality and lifetime
Manufacturers of PCBs are continuously looking for ways to reduce cost of production and to increase quality and lifetime of the PCBs. Temperature plays a critical role in this endeavor, and measuring the temperature becomes more and more important.
Relevance of temperature
Temperature is without any doubt an important element, if not the most important element of not only reliability, performance but especially safety in PCBs. If, during manufacturing or normal operation, parts of the PCB or components on the PCB reach a too high or too low a temperature, this will lead to defects and in worst case scenario damage of the PCB. Heat can be caused by
- a component mounted to the PCB
- inadequate ventilation
or
- drilling and soldering during assembly.
Over- or underheating will lead to defective boards and therefore will increase waste, will increase labor and therefore costs.
Testing of PCBs
Temperature related defects in PCBs in the field can potentially have devastating consequences. To prevent PCBs from malfunctioning in the field, functional tests are performed on EACH individual PCB under not only normal but also strenuous operating conditions. To perform these tests, test fixtures are designed and used with the goal to simulate the environment in which the actual assembly will be performing. To help save money, PCB test fixtures are designed to test the entire assembly, as opposed to only focusing just on one area or (set of) component(s). This eliminates the need to create duplicate testing operations and provides a more thorough test down-stream in the process itself. It also helps to save time by providing comprehensive functional test interface solutions designed to work in concert with in-circuit testing and other test systems and integration. Quality functional test interface solutions can test up to 100 percent of the products before they are shipped for the best results.
Temperature sensors form an important part of PCB test fixtures, to assure that
- specified acceptable temperature ranges of PCBs and components are met, and
- malfunctioning in the field is prevented.
Elite Interface
Elite Interface, based in the UK, is specialized in designing and producing test fixtures for functional testing of PCBs. In this example, they have designed a test fixture for a PCB used in the automotive industry which is performed at the end of the PCB manufacturing process. The client tests the end circuit of the board, electrically touching the full board of capacitors, conductors, IC’s and also diode, therefore conducting a component test by making sure that there are no opens or shorts of all the components on the board.
The diode serves as a built-in temperature sensor that serves as a safety device to set off an alarm if PCB temperatures get too high. During testing in the test fixture, this diode needs to be tested for accuracy. This is done by measuring the diode temperature with an IR temperature sensor during operational cycles and reading out the diode outputs for comparison. Only if the diode reading turns out to match the IR sensor reading, the PCB can pass the functional test. This is to verify that the board meets the specification and therefore operated within certain temperatures ranges.
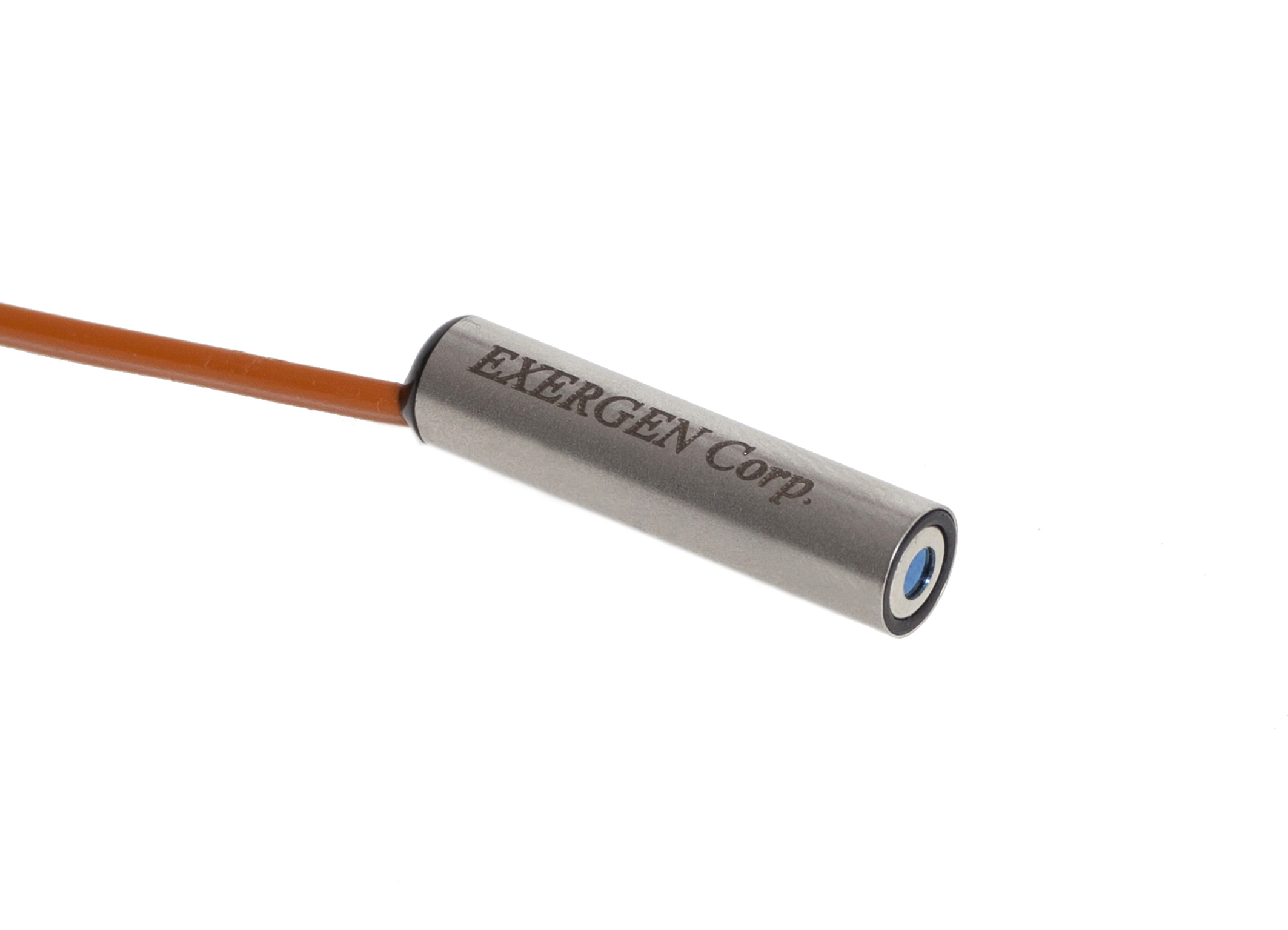
Why an IR sensor?
An IR sensor is the only way to reliably and quickly measure temperature in test fixtures. In most cases, 100% testing is performed on PCBs as each individual board needs to be approved. This means a high throughput, and very short test cycles are required. This can only be achieved by the use of non-contact IR sensors: these have much faster response rates than contact probes, and eliminate the need to physically connect the probe to the board in each cycle – which would be very time consuming and prone to measurement errors.
Elite interfaces has selected Exergen’s Micro IRt/c to measure the diode temperature, because of its small size, cost effectiveness, fast response time (50ms), reliability and long term stability.