Robotic Pipeline Repair
Robotic pipeline repair with the help of Exergen’s micro IRt/c Sensors
Sewage
Underground utilities are any public service infrastructures installed beneath the ground surface, like lines used for sewage systems (water/ wastewater pipelines). Sewage systems consist of pumps, pipes, or mains used for collecting wastewater within an entire network. Good working sewer systems are an extremely important and essential part of the urban infrastructure. It is crucial to maintain sewage systems properly, otherwise, they can be harmful to the population and the environment.
Proper maintenance of sewage systems prevents waterborne diseases from being spread. Next to this, it is also vital for protecting water resources. Without any doubt, it is imperative to understand the working of these systems and how they can be maintained in an efficient manner. Therefore, having a continuous program of sewer rehabilitation is of correspondingly high importance whilst keeping costs and labor as efficient as possible.
Sewage repair
Traditional pipeline repair requires that the section of the pipe that is damaged is excavated and repaired or replaced by a technician. This method has many disadvantages: the damaged pipe needs to be taken out of commission and excavated. This requires the use of heavy equipment and the area around the excavation needs to be sealed off, resulting in the closing of roads, sidewalks or other areas. This in turn has effects on the traffic flow, accessibility of (shopping) areas etc. This made the repair of sewage pipes an expensive, time consuming and bothersome task with many negative side effects.
Trenchless sewer rehabilitation technology by ProKASRO
The German company ProKASRO has developed a fully automated method to repair sewage pipes without the need to excavate. To inspect and repair pipes from within, technicians use robots with cameras attached that can be entered into the damaged pipe. Technicians operate them from above ground and watch the live feed on their closed-circuit television to see where the pipes are damaged and where they will need to make repairs.
ProKASRO is a full range manufacturer and supplier for sewer rehabilitation. Their KASRO robot systems are available for different pipe diameters from DN 100 to DN 1200 and they can be combined as required. Various tool attachments permit the sewer robots to perform milling, grinding, filling, molding and injection operations. They can also be used for positioning balloons and installation of top hat profiles and liners for lateral connections. All rehabilitation work is managed and monitored from a rehabilitation vehicle which can be placed at a convenient location nearby. Using sewer rehabilitation robotic systems is significantly easier and cheaper than replacing sewer pipes using traditional methods.
The robots allow for damage diagnoses and repairs to be carried out without excavation work, traffic obstructions or noise. Working within short rehabilitation timeframes ensures that it is not usually required to block off the sewer during rehabilitation work. This makes sewage repair easier, quicker and cheaper without the negative side effects of excavating broken pipes.
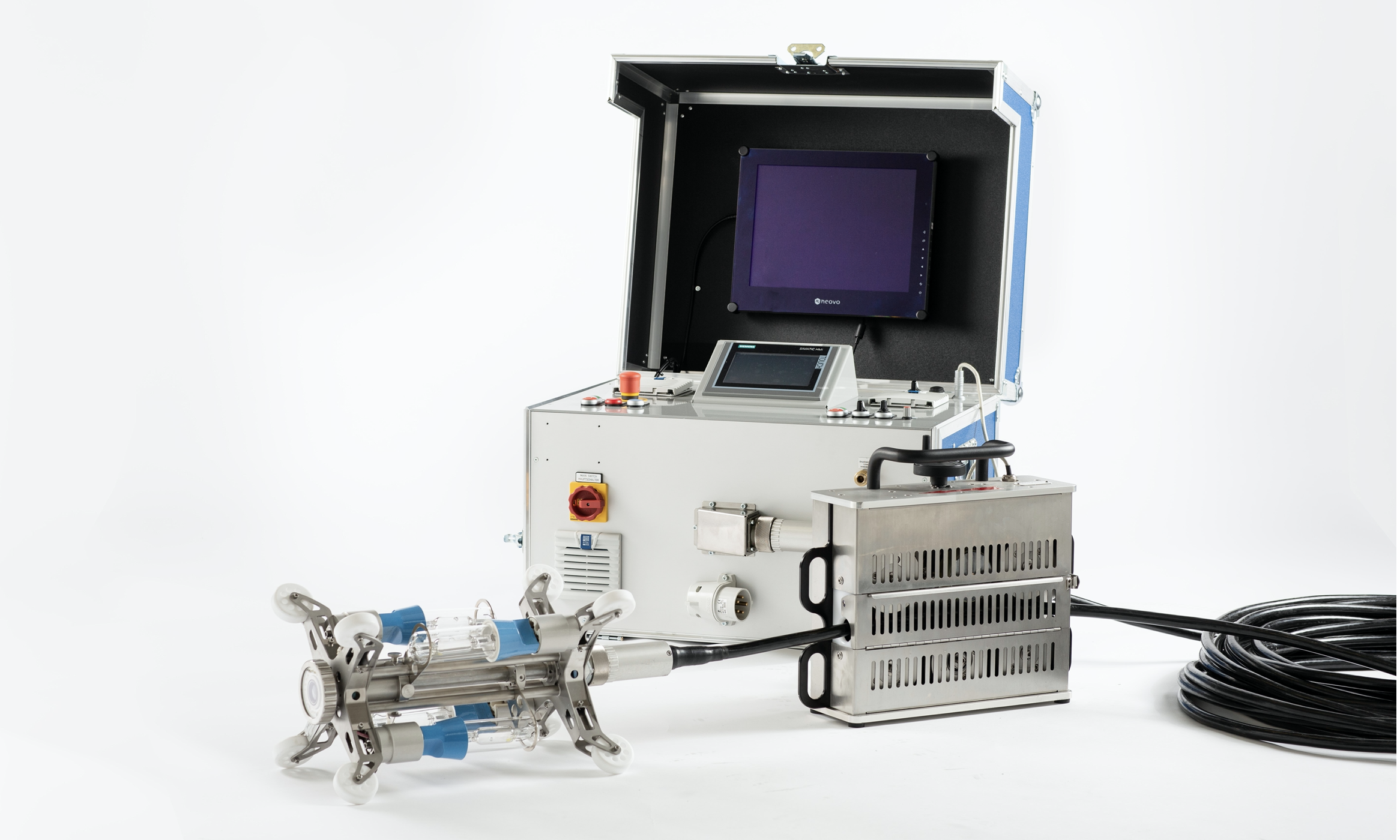
Temperature in pipe repair
From an area where the sewage is accessible, a liner is being pulled in the sewer with the help of a winch. The UV liner is impregnated with a resin that is curable with UV light. Once the liner is positioned correctly within the patch of sewage pipe that needs repair, it is pressurized so it expands against the inner wall of the pipe. UV light sources are entered into the liner and they illuminate the inner wall of the hose. When UV light encounters the resin, a chemical reaction takes place which hardens the resin. The newly formed layer of hardened resin now forms a novel inner layer of piping that is impenetrable for fluids. The damaged sewage pipe is now repaired.
In order to guarantee high quality of the repair, the duration of the exposure to UV light of the resin is crucial: if the exposure is too long, the cured material can become brittle. If the exposure is too short the curing process has not been completed and parts of the laminate can still be liquid. In both cases there is a risk a leak might occur.
The duration of the exposure can be monitored and controlled by measuring the temperature of the resin during the curing. The temperature of the resin is indicative for the extend of the curing: once all the resin is cured, continued exposure to UV light will cause an increase in temperature. So, by monitoring the temperature of the resin carefully, the operator will know when the resin is completely hardened and therefore, the curing process can be stopped.
Advantages
Using sewer rehabilitation robotic systems are significantly easier and cheaper than replacing sewer pipes using traditional methods. ProKASRO uses its robotic systems for sewer rehabilitation, temperature measurement and UV technology for the underground sewer system enabling it to be safeguarded whilst maintaining ecological, hygienic and technical standards.
Exergen’s proprietary technology includes the smallest available IR sensor – the Micro IRt/c. The sensor does not need a power supply because it is self-powered. It consists of only passive components and therefore does not drift, making the sensor very stable, durable and accurate. Another advantage is that the sensor does not need periodic recalibration, as all powered sensors do. This means that ProKASRO has no maintenance on the sensor when their robotic systems are in the pipes. Combine this with the fact that the IRt/c is able to withstand high ambient temperatures AND is not sensitive for UV light, and you clearly get a winner.
Exergen’s non-contact IRt/c sensors are extremely accurate. The IRt/c sensor makes it possible to measure the exact temperature during the curing process, with a resolution of approx. of 0.0001°C and a repeatability error of 0.01°C. This ensures ProKASRO exactly knowing at what temperature to stop. Doing this and being able to control it, they increase the efficiency and the quality outcome of the total curing process turning it in a highly cost effective procedure.
Case Study
September 2020, ProKASRO and one of their partners worked on a UV shaft rehabilitation system in Brno / Czech Republic. Three manholes, each with a diameter of DN 1000 and lengths of one to three meters, were rehabilitated with brand new products from technology and liner manufacturers in Brno and Budweis. The combination of the Brandenburger Liner “BBS.8 UV”, specially designed for manhole rehabilitation, together with the new KASRO UV manhole rehabilitation system led to a smooth and fast curing with perfect results. ProKASRO designed the 4 x 1000W UV light source core with camera and 2 of Exergen’s infrared temperature sensors. A separate control unit in a small flight case with logging, temperature, and pressure measurement as well as a single packer DN 500 with straps for the crane suspension for easy insertion into the shaft were included in the mobile UV system. With this system, manholes can be restored to an excellent condition. If there are heavily damaged manholes with fractures, cracks and other types of damage, rehabilitation using UV technology whilst keeping temperature management under control via accurate IRt/c sensors of Exergen, is the more cost-effective and environmentally friendly alternative to excavation and complete manhole renewal. With a pulling speed of 25 cm per minute, the actual renovation process including lowering the core, igniting, and pulling it up again with curing was completed after ten minutes. The entire process from arriving at the construction site, preparing the shaft, installing the liner, calibrating the liner, lowering the UV core in the manhole, keeping track of the temperature whilst curing was completed in just two hours. The robots use the temperature sensors to send readings from within the pipeline that records the temperature of the UV pipe wall’s integrity and thickness. The information helps the operators to know if the line is salvageable or needs to be replaced. Repairs are made using a rotating nozzle that applies sealant from any angle. Until recently, pipeline repair was a time- consuming process that involved getting up close and personal with the area of concern – but advances in robotic inspection technology now promise to cut the time it takes to repair pipelines and the staff required to do it.