Gas Abatement Systems
IR sensors for accurate temperature monitoring in high-end exhaust gas abatement systems
General Information
Exergen’s sensors are used in high-end exhaust gas abatement systems around the globe. Many of the special gases used in semiconductor wafer processing and other manufacturing industries are either toxic, pyrophoric or corrosive. Unused process gases and hazardous by-products must be removed from exhaust lines efficiently and safely for safety and to ensure compliance with regulatory emission standards.
The unused gases are chemically converted to safe, stable solids in absorber columns. These columns consist of solid beads that (often) contain proprietary chemicals that react with the exhaust gasses, resulting in slight temperature increases. This process starts at the bottom of the column, and during the lifetime of the column (several months generally) it moves upward. Once all beads have fully reacted, they can no longer extract the hazardous by-products from the gasses and must be replaced. The time remaining before a column needs replacement can be monitored using temperature sensors that detect increased heat within the column, signaling when it has reached the column top.
The absorber columns are specifically designed to clean gasses in a manner that meets customer specifications. However, if the gasses have higher concentrations of gasses or contain components other than those specified by the customer, there is the potential for an exothermic reaction that can overheat the column swiftly, risking dangerously high pressure levels and hazardous gas leaks. Fortunately, this scenario can be detected early and prevented by shutting down the system before it overheats.
The Optimal Solution
Thermal sensors are an ideal solution to monitor column temperatures, allowing operators to determine when a column should be replaced and if it is at risk for overheating from exothermic reactions. Downtime of these systems is very costly so should be limited to the minimum therefore the ideal sensor for this application should require zero recalibration or maintenance. Sensors used in this setting must also be extremely accurate in order to maximize the column’s lifetime and avoid overheating. Finally, since the sensors are used in potentially hazardous environments, in which flammable conditions might occur, they must be intrinsically safe.
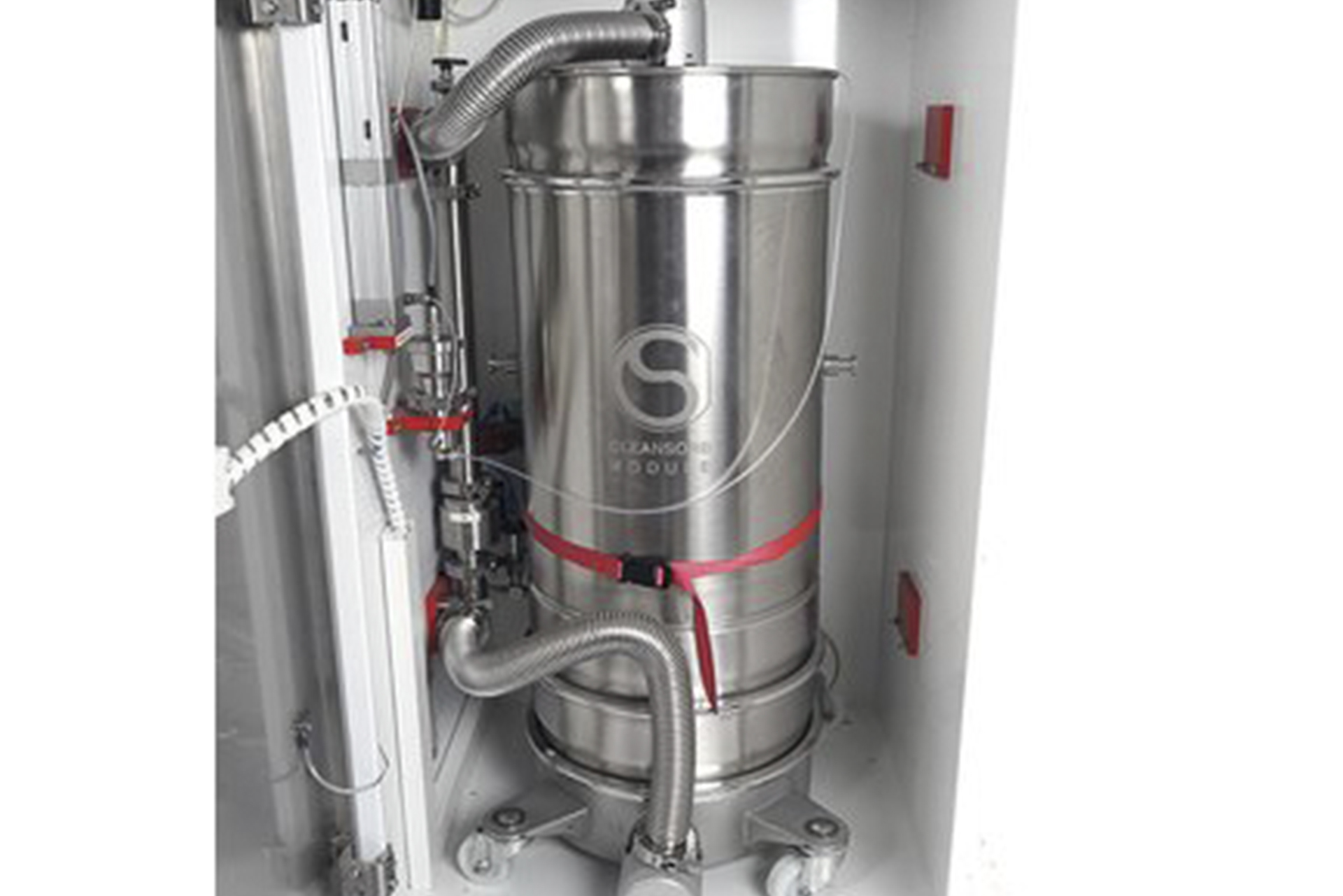
Why Exergen IR Non-Contact Sensors?
Exergen IRt/c sensors are non-contact sensors that don’t need to be replaced or remounted when a column is replaced. They are passive devices, resulting in:
- zero in-field recalibration or maintenance, which considerably limits system downtime
- intrinsically safe in potentially flammable environments
- very fast and accurate to reliably monitor safety and lifetime of the columns
- very small, easy to mount on any size of column
Commercial Advantages
- Accurate temperature monitoring prevents column overheating and optimizes safety
- Allows for easy and swift replacements of columns
- Provides reliable data on when a column is exhausted and needs replacement – not too early, not too late
- No downtime added by the sensor, no maintenance or calibration needed