Ablation Cooling System
Exergen’s sensor solution essential component of ablation, cooling system
General Information
A subset of surgical devices, including surgical drills, cutters and ablation probes, employ heat to incise or cauterize tissue. When using surgical instruments that employ heat, it is a challenge is to ensure that those portions of the instrument that do not need to conduct heat remain cool enough to avoid any negative side effects. In most cases, the necessary cooling can be achieved using pressurized gas or liquid, along with thermal sensors that measure temperatures.
This application note discusses an instance in which thermal management was employed in a setting where gas was used to cool an ablation probe, but the concepts can be applied to any number of other instruments and to instances that use liquid, rather than gas for cooling.
Challenges
Exergen recently worked with a medical device company challenged with the need to apply enough energy to an ablation probe’s tip to successfully conduct a procedure while ensuring the probe’s shaft remained cool enough to avoid complications. The company used a CO2-based cooling system equipped with Exergen’s thermal management sensor. The cooling system was housed on a compact, portable platform, and included CO2 tanks. The thermal sensor was an essential component of the cooling system, providing the means to measure a CO2 tank’s temperature to gauge its capacity and ensure it maintained sufficient pressure during procedures. If the CO2 tank in the cooling system lost pressure, it would fail to cool the ablation probes and could cause serious injury to the soft tissue.
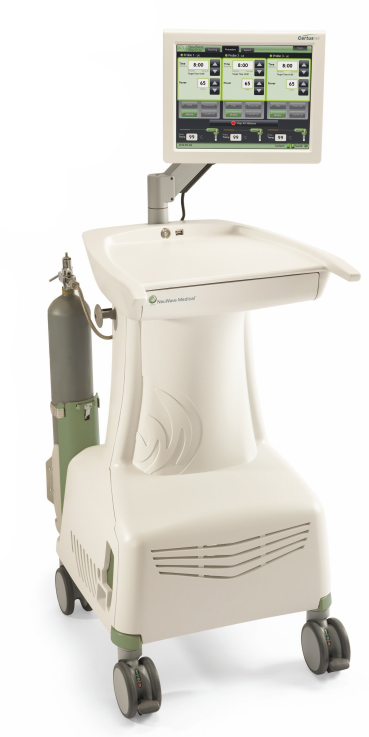
The Optimal Solution
The optimal thermal management solution for this application was Exergen’s high speed, non-contact micro IRt/c.SV temperature sensor. Contact sensors weren‘t well-suited to the task because they need as much as 15 seconds to acclimate before registering an accurate measurement. This would have caused unnecessary and potentially dangerous delays when empty CO2 tanks had to be replaced, because the contact sensors would need to be positioned on the tanks and then require time to acclimate.
The ideal sensor for this cooling system also needed to provide real-time measurements. Another important consideration for this cooling system was a sensing device that was easy to mount, yet wouldn’t be dislodged if it protruded outside of the platform footprint. It was also important to select a device that would eliminate the area around the tank from its field of view, since an inclusion of that view would cause measurement errors. Also, the sensor needed to account for the fact that the tanks used for the application differed in size and material from one hospital to the next. Some tanks were painted, some rusty, and some shiny aluminum – yet the measurements couldn’t be affected by the differing reflective properties of the tanks.
Why Exergen IR Non-Contact Sensors?
With a size of just 0,64 cm (¼”) diameter and 3,73 cm (1.47”) long, the Exergen side view non-contact micro IRt/c.SV sensor integrated easily, securely and unobtrusively into a bracket on the CO2 tank. In this application, the bracket served the dual purpose of housing the sensor and preventing radiation from surrounding heat sources (for example, a surgeon walking by) to reflect off of the CO2 tanks surfaces and create measurement errors.
Since it is a non-contact sensor, the micro IRt/c.SV’s location on the cooling system’s cart remained constant and that constancy eliminated the risk of misaligning cylinders during replacement and ensured an accurate temperature reading at all times. The sensor’s < 50 millisecond response time provided real-time measurement and experienced no downtime in temperature detection following cylinder replacement.
Commercial Advantages
- Fast results so no machine downtime
- Guaranteed patient safety under all conditions
- Re-useable solution and this cost effective
- Sensor does not need service or calibration in the field, saves cost, more reliable